Effective boiler water treatment is essential for operational efficiency, safety, and longevity of boiler systems. Central to this is the use of carefully selected chemicals, each serving specific purposes within the treatment process. Understanding the types and functions of these chemicals ensures that boiler systems run smoothly, avoiding common issues such as scaling, corrosion, and fouling.
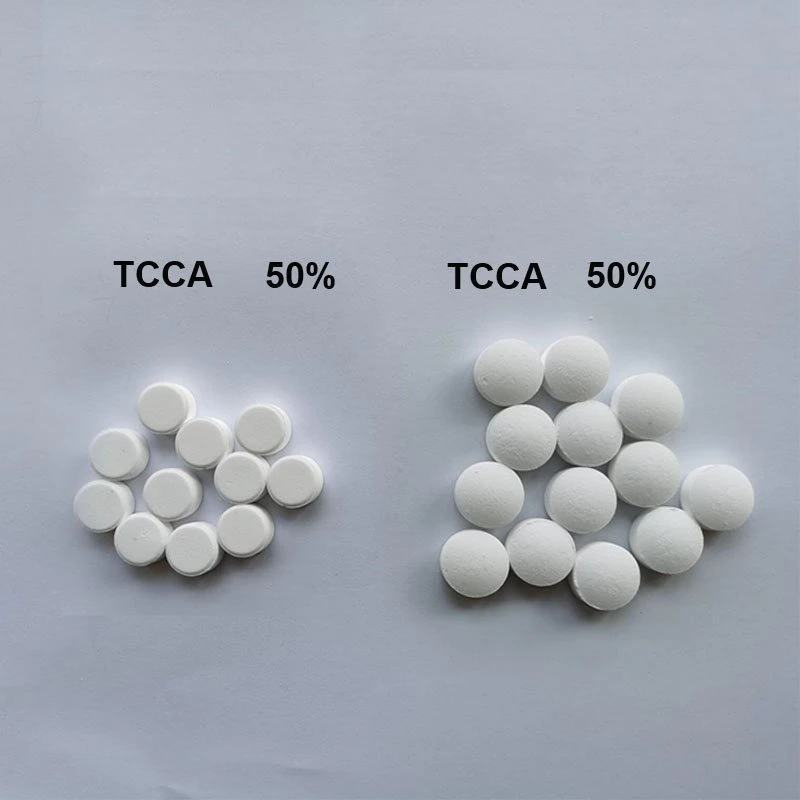
One primary category of chemicals used in boiler water treatment is oxygen scavengers. Oxygen in boiler water can lead to significant corrosive damage. Sodium sulfite is a commonly used oxygen scavenger, ideal for low to moderate pressure boilers. On the other hand, high-pressure boiler systems benefit from volatile oxygen scavengers such as hydrazine or DEHA (Diethylhydroxylamine), which decompose at high temperatures, and help maintain the integrity of the metal surface throughout the system.
Corrosion inhibitors are another crucial group of chemicals. Phosphates and polyphosphates are frequently utilized to control the alkalinity levels in boiler water, thereby preventing acidic corrosion. Compounds such as phosphoric acid derivatives help in forming protective films on metal surfaces, safeguarding the system from corrosion.
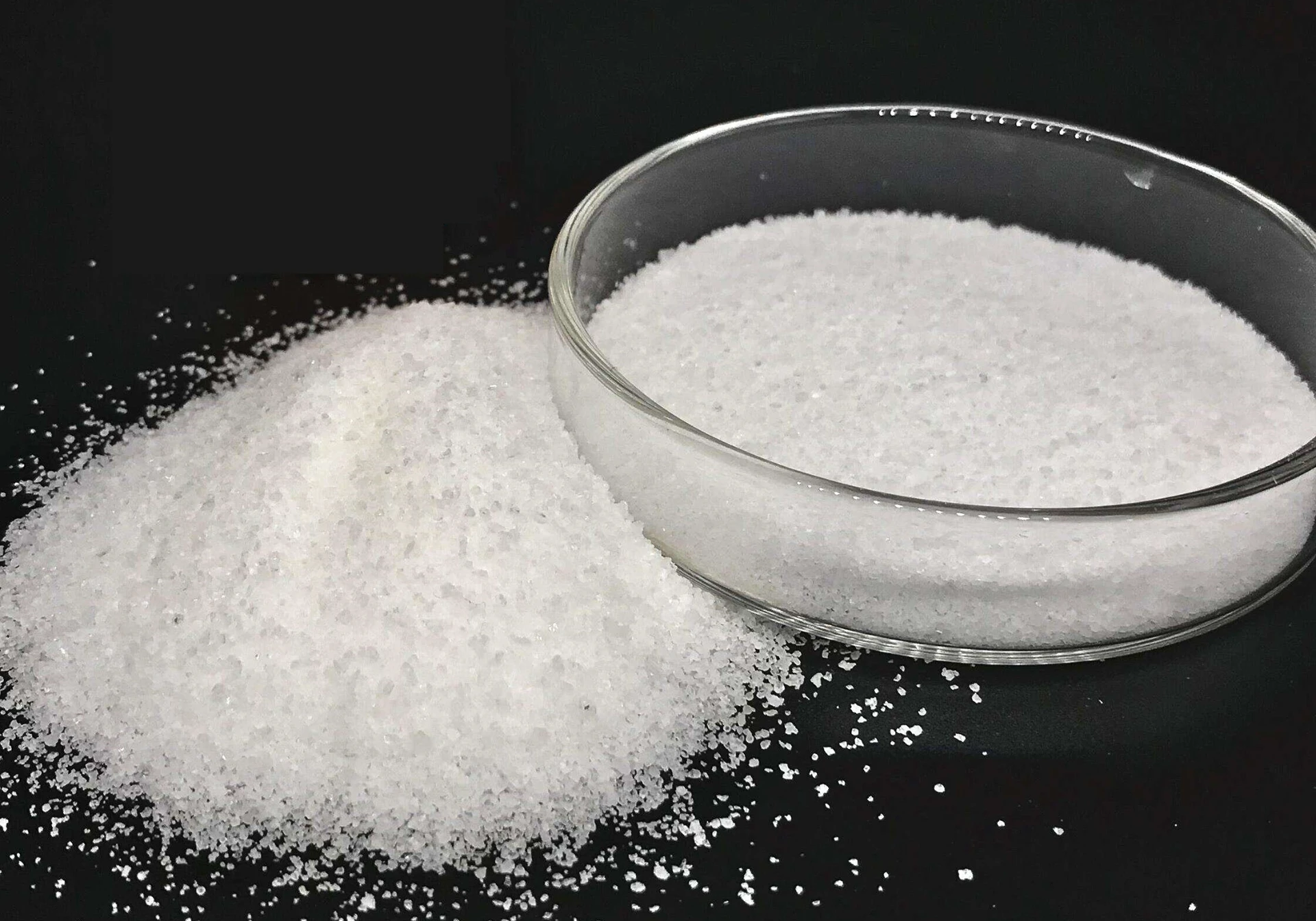
Scale inhibitors, meanwhile, prevent the accumulation of mineral deposits, which can obstruct heat transfer and reduce efficiency. Chelating agents like EDTA (Ethylenediaminetetraacetic acid) are popular for binding with calcium and magnesium ions, thereby keeping them in a dissolved state. Similarly, polymers are used to prevent the coagulation of scale-forming minerals, ensuring that they are dispersed rather than deposited.
For controlling pH levels, neutralizing amines like morpholine, cyclohexylamine, and DEAE (Diethylaminoethanol) are employed. These chemicals neutralize carbonic acid formed from dissolved CO2, preventing damage to condensate return lines. Their volatility also allows them to travel with the steam, providing protection throughout the system.
chemicals used for boiler water treatment
Further, anti-foaming agents are essential in maintaining boiler water quality. Foaming can lead to carryover of water with steam, causing deposits on turbines and other downstream equipment. Silicone-based defoamers are commonly used, as they destabilize air bubbles and prevent foaming, ensuring that only pure steam exits the boiler.
In addition to these, sludge conditioners play a role in preventing the setting of suspended solids. The use of tannins and lignins modifies the character of any sludge formed so that it remains non-adherent and can be easily removed during blowdown processes.
The integration and balance of these chemicals must align with boiler operating conditions and water characteristics. Periodic monitoring and adjustment of chemical dosages are vital practices. This precision ensures that treatment chemicals are effective without introducing additional issues. Professional expertise is advised in selecting and managing treatment chemicals to avoid adverse reactions and ensure regulatory compliance.
Implementing a robust chemical treatment regime not only extends the operational lifespan of boiler systems but also significantly curtails repair and maintenance costs. Ultimately, it ensures a reliable, efficient energy supply crucial for multiple industrial processes.