Creating sodium chlorate involves a fascinating blend of chemistry and industrial expertise, reflecting both the complexity and beauty of chemical processes. As an ingredient used in various applications, from bleaching paper to producing herbicides, sodium chlorate's importance in the industrial chemistry landscape cannot be overlooked. Understanding its production allows for improved processes, optimized safety, and enhanced sustainability.
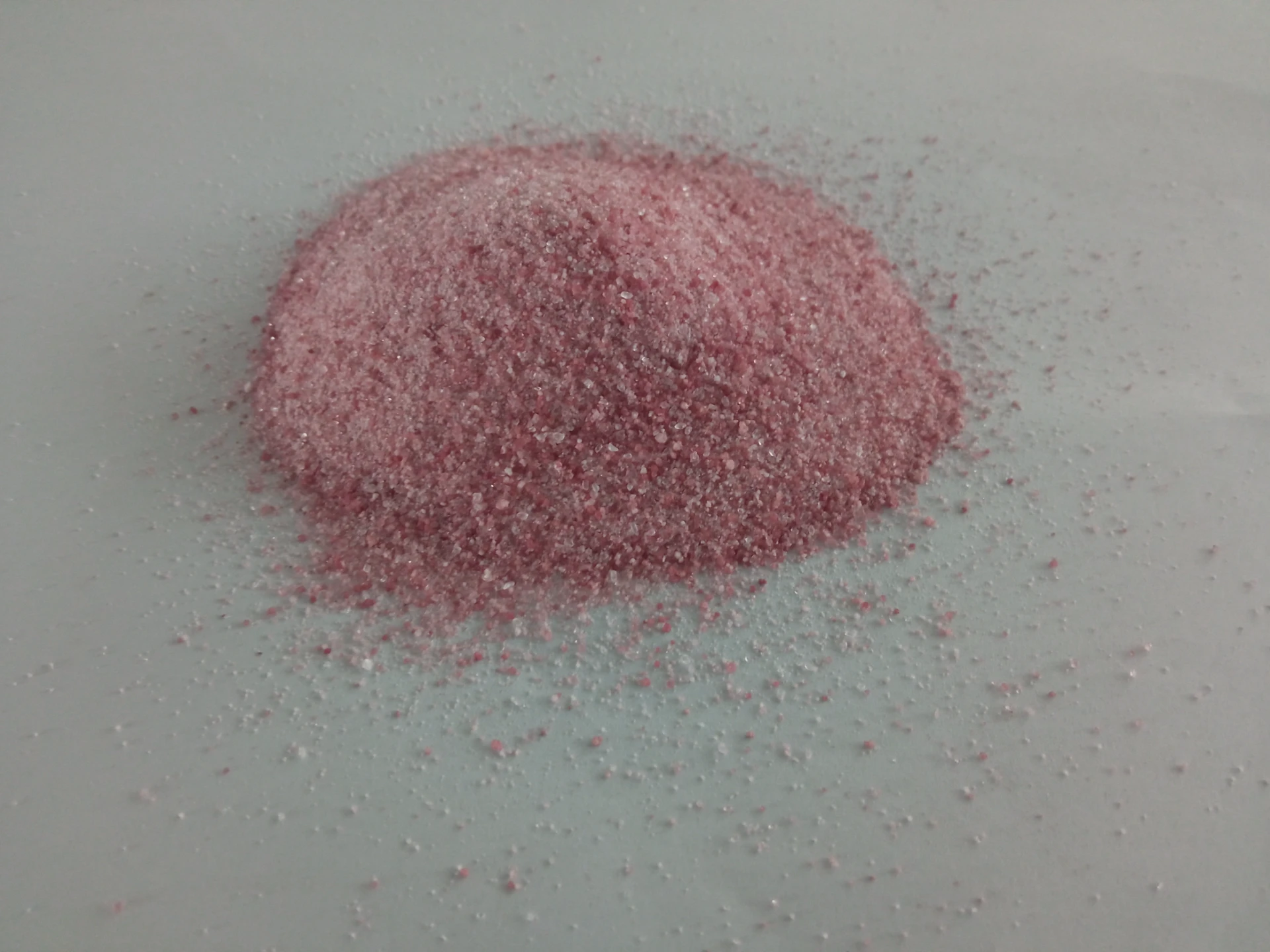
The production of sodium chlorate primarily involves the electrolysis of sodium chloride (table salt) in water. This seemingly simple process actually requires a nuanced understanding of chemistry and engineering to ensure efficiency and safety.
At its core, the production process centers around an electrolytic cell. Within this cell, an electrical current is passed through the saltwater solution. This electrical energy dissociates the sodium chloride into its constituent ions sodium (Na+) and chloride (Cl-), while also splitting water into hydrogen (H2) and oxygen (O2). The reactions at the electrodes lead to the formation of sodium chlorate, primarily through the intermediate formation of sodium hypochlorite, a reaction catalyzed by specific cell conditions.
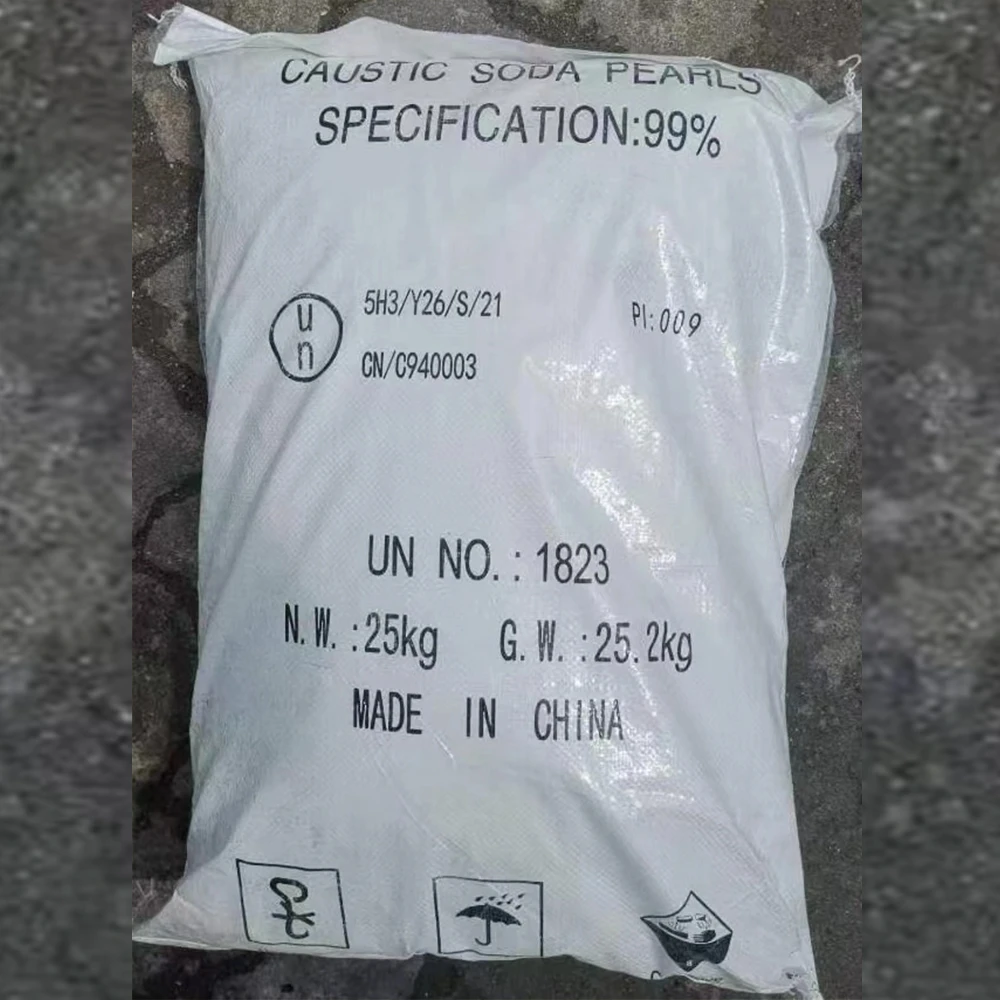
Maintaining precise conditions within the electrolytic cell is crucial. The temperature, pH, current density, and electrolyte concentration all influence the efficiency and safety of the sodium chlorate production. Typically, temperatures are maintained around 90-98°C, while the pH is carefully controlled to be highly alkaline, around 11. The efficiency of chlorate formation can vary, with roughly 55-60% of the electrical energy converted into useful product under optimal conditions.
Safety remains a paramount concern in the production of sodium chlorate. The generation of hydrogen gas during electrolysis is a notable hazard due to its explosiveness. Strict ventilation and containment procedures are necessary to prevent hydrogen accumulation. Moreover, the strong oxidative properties of sodium chlorate itself require cautious handling and storage practices to mitigate risks associated with inadvertent reactions.
making sodium chlorate
Sustainability and environmental considerations are increasingly at the forefront of sodium chlorate production. The process is energy-intensive, leading many companies to explore renewable energy sources to power the electrolysis. Additionally, advances in membrane technology for electrolytic cells can increase energy efficiency and reduce raw material consumption. Efforts are also made to recycle and treat waste generated during production, including managing chlorate-laden effluents in an environmentally responsible manner.
The application of sodium chlorate extends beyond mere production to its role in various industries. In the pulp and paper industry, its use as a bleaching agent is indispensable. Its oxidative strength efficiently breaks down lignin, the component of wood that binds cellulose fibers, without compromising the integrity of the fibers themselves. This results in whiter, brighter paper products that are fundamental to countless consumer goods.
In addition to bleaching, sodium chlorate finds utility as an herbicide. Its ability to disrupt photosynthesis in plants makes it a popular choice for controlling weeds in agricultural settings. However, this application requires diligent adherence to environmental regulations to prevent adverse ecological impacts, ensuring its benefits do not outweigh its risks.
Ultimately, the production of sodium chlorate is an intricate process that embodies the principles of chemical manufacturing and industrial scale synthesis. By optimizing the parameters of this process, confronting safety challenges, and addressing sustainability concerns, industries can continue to harness the considerable benefits of sodium chlorate efficiently and responsibly. For those seeking to enhance their understanding or refine their production capabilities, engaging with the latest research, technological advancements, and industry best practices is crucial.
As technological innovations continue to revolutionize chemical manufacturing, the journey of sodium chlorate from salt to finished product will undoubtedly evolve, driven by the perpetual quest for efficiency, safety, and environmental accountability.