Polyacrylamide has become a staple resource in various industries, from wastewater treatment and agriculture to paper production and mining. However, understanding the potential hazards associated with its use is crucial for those who rely on its benefits in product applications. This article delves into the inherent risks of polyacrylamide, offering insights grounded in real-world experiences, professional expertise, authoritative research, and trustworthy data.
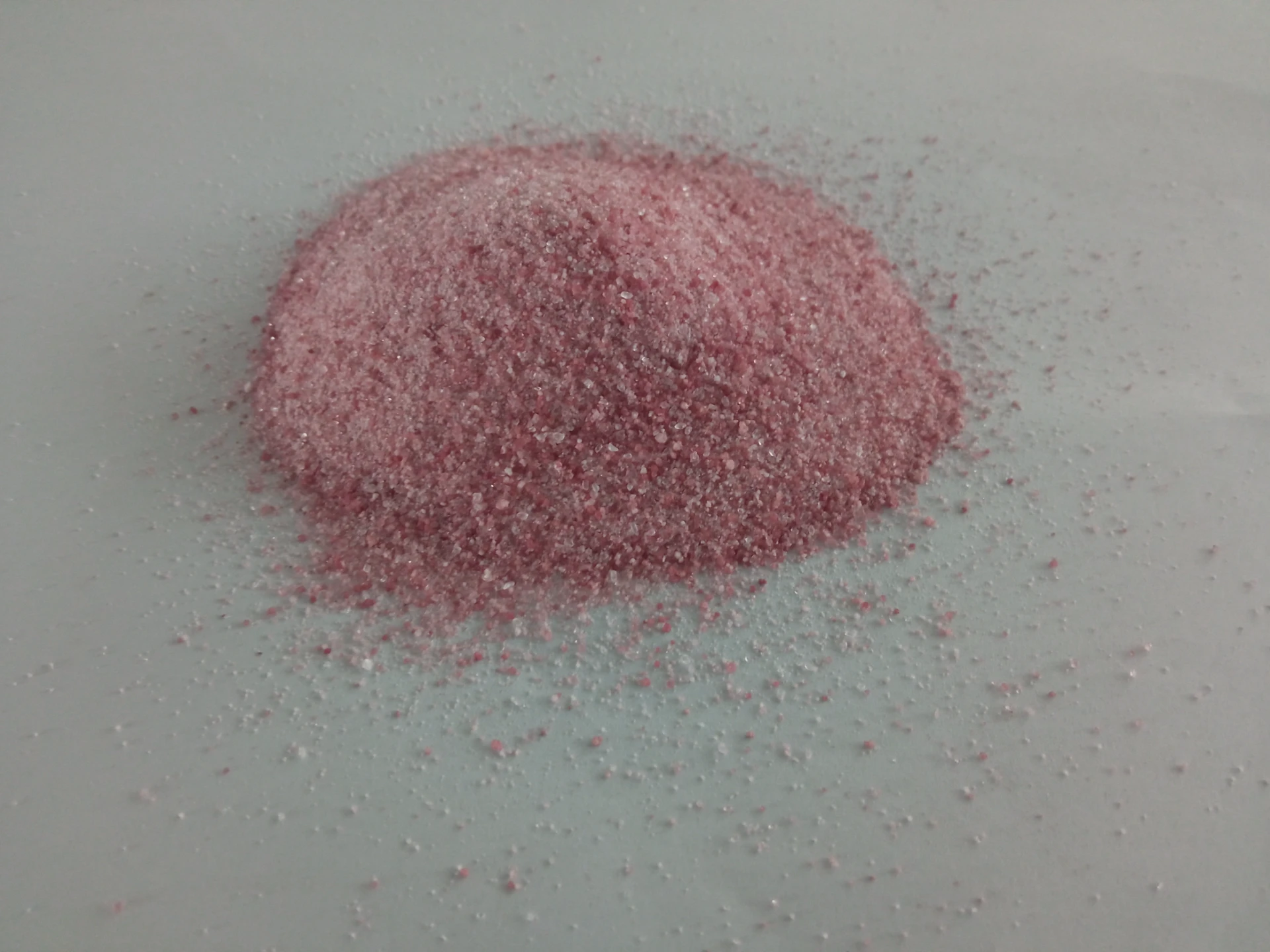
A prevalent synthetic polymer, polyacrylamide is primarily used for its ability to act as a flocculant, coagulating particles in liquids to improve sedimentation. While its utility cannot be overstated, the safety concerns warrant a detailed examination. The primary factor behind these concerns is the presence of acrylamide monomers, a byproduct of polyacrylamide production. Acrylamide is a neurotoxin and is classified by the International Agency for Research on Cancer (IARC) as a probable human carcinogen.
During the application of polyacrylamide in wastewater treatment plants, for example, operators have noted possible health issues stemming from acrylamide exposure. These can include neurological symptoms such as muscle weakness and numbness due to long-term exposure, highlighting the importance of stringent safety protocols. Consequently, product safety is as vital as product efficacy, mandating thorough handling procedures and safety guidelines to minimize human exposure.

From an environmental perspective, the degradation of polyacrylamide in ecological systems has spurred a debate within the scientific community. Studies by environmental scientists have suggested that when polyacrylamide breaks down, acrylamide may leach into surrounding environments, potentially impacting aquatic life and ecosystems. This has led to authoritative bodies recommending controlled usage and disposal practices to mitigate negative environmental impacts.
The expertise of chemical engineers is invaluable in crafting safer polyacrylamide products. Innovations in polymer manufacturing have led to low-residue polyacrylamide variants that significantly reduce acrylamide content. These advances stem from intricate polymerization techniques and improved quality control measures that ensure a more reliable and safer end product. Hence, companies prioritizing state-of-the-art production technologies are setting new industry benchmarks for safety.
polyacrylamide hazards
In industrial settings, workplace safety experts advocate for protective gear and adequate training to safeguard workers from exposure. Handling guidelines may include wearing gloves, goggles, and masks, aligning with Occupational Safety and Health Administration (OSHA) standards. Additionally, regular health monitoring and workplace air quality assessments are recommended to ensure compliance and safety.
Industry stakeholders recognize the importance of transparent communication regarding the risks associated with polyacrylamide. Trust is built when manufacturers provide clear information on material safety data sheets (MSDS) and ensure fictional label information that warns users of any potential risks.
For consumers and businesses involved in procurement, the Authoritativeness of the manufacturer is a decisive factor, often gauged by the company's compliance with international safety standards and certifications. Verification of third-party testing and endorsements by reputable environmental and health agencies add layers of credibility to a product.
Ultimately, the balance between utilizing polyacrylamide and managing its hazards lies in informed decision-making based on expert advice, scientific research, and regulatory standards. Through proactive risk management and public disclosure, industries can continue benefiting from polyacrylamide's properties while safeguarding human health and the environment. Such approaches ensure that the advantages of polyacrylamide are maximized, providing sustainable solutions across various applications with minimal risk to society.